In Kazakhstan, the year 2025 has been declared the Year of Skilled Trades. As part of this initiative, the national atomic company "Kazatomprom" organized a press tour to its subsidiary, LLP "SP Inkai," from February 10 to 13, 2025, reports the correspondent of the business information center Kapital.kz.
JSC "NAC "Kazatomprom" (CAP) is the national operator of the Republic of Kazakhstan for the export and import of uranium, rare metals, as well as nuclear fuel for nuclear power plants, which provides the company with priority access to one of the largest resource bases in the world. Since 2010, CAP has been the global leader in uranium production, and since 2018, it has held the top position worldwide in uranium sales.
"Kazatomprom" manages a total of 27 deposits and 14 uranium mining enterprises. One of these, LLP "SP Inkai," was established in March 1996. "Kazatomprom" owns a 60% stake in the company, while Cameco Corporation (Canada) holds 40%. The total number of employees at SP Inkai is 811.
About Uranium Mining
SP Inkai extracts uranium using the underground leaching method (ULM) at site No. 1 of the Inkai deposit in the Sozak district of the Turkestan region. The journey from Shymkent to the shift camp near the mine takes about 7-8 hours. With no stops, it can be done in 6 hours, the company shares.
On one of the days of the press tour, journalists visited the territory of the geotechnological polygon (GTP), where the extraction of natural uranium using the ULM method takes place. "Today, this is the most environmentally friendly, cost-effective, and efficient method of uranium extraction," says Stepan Tretyakov, head of the extraction department at SP Inkai.
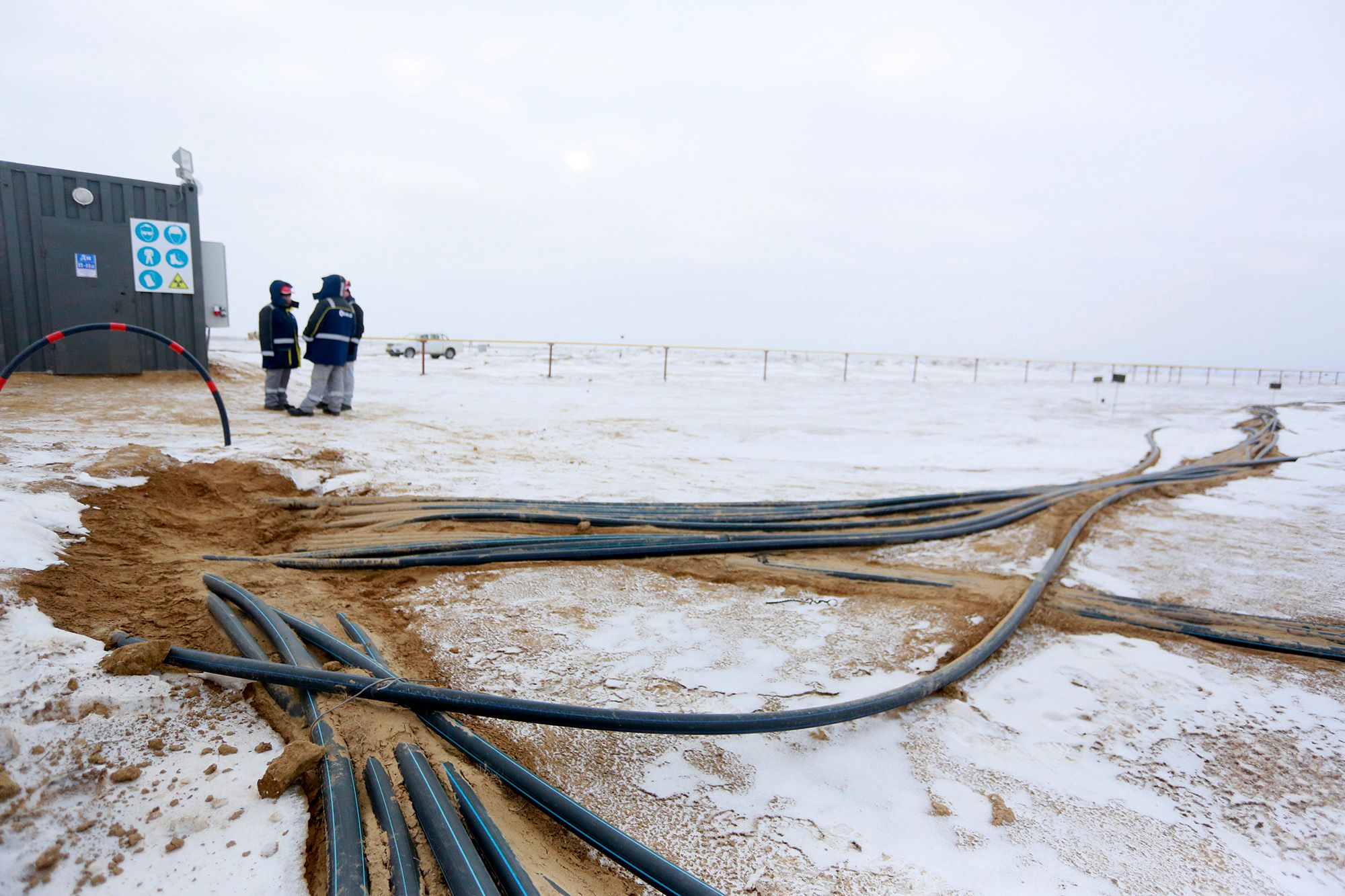
Uranium is extracted from depths of 350 to 500 meters underground – geotechnological wells are constructed. Drilling one well takes about a week. "At any given time, there are about 3,500 wells operating across the entire geotechnological polygon, the majority of which are injection wells (110 mm in diameter), and one-third are extraction wells (225 mm in diameter)," the speaker states. Weakly acidic sulfuric acid solutions are injected through the injection wells, while solutions saturated with natural uranium minerals are extracted through the extraction wells.
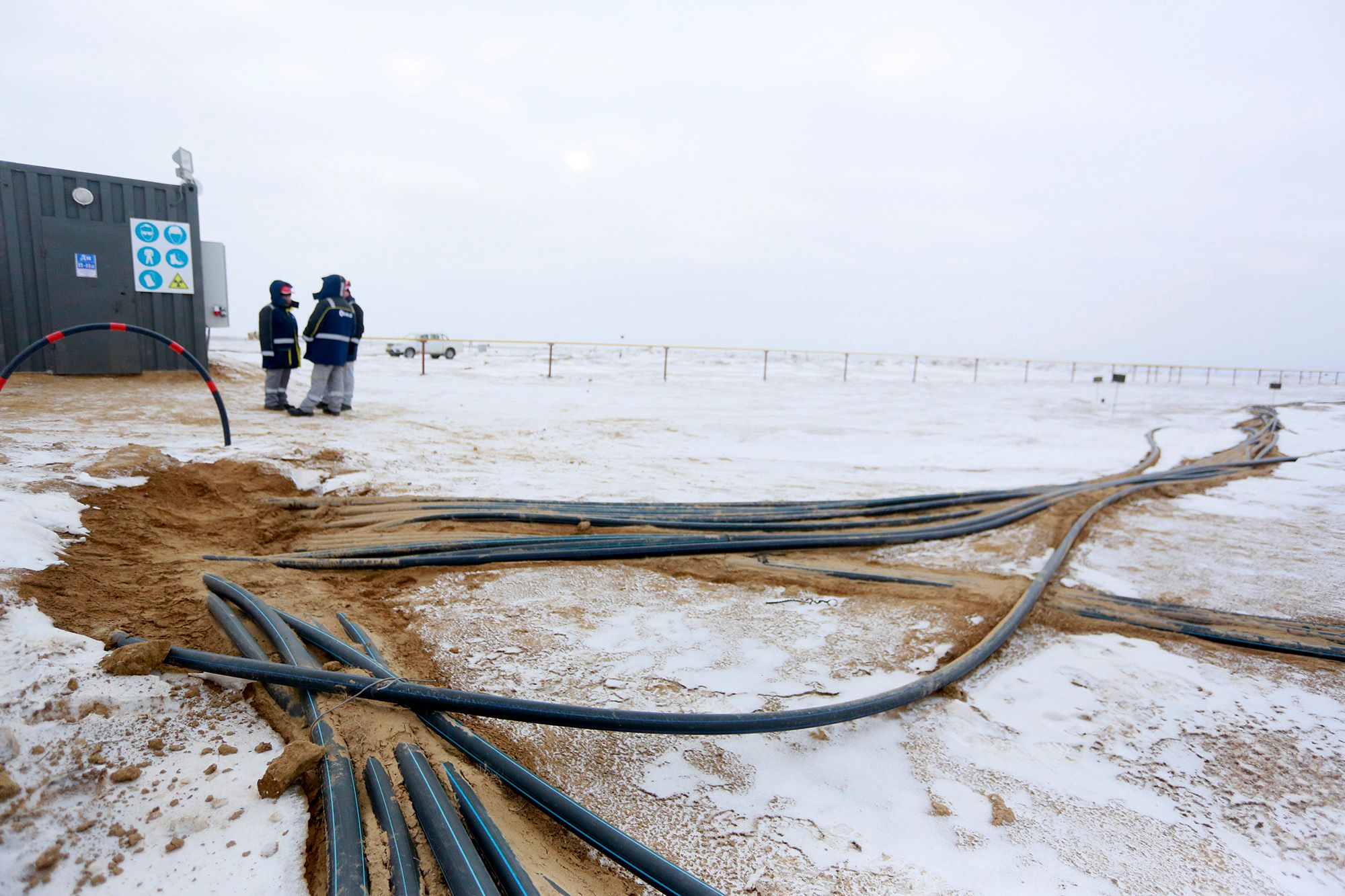
Thus, uranium is in a dissolved state. Stepan Tretyakov emphasizes that this method is the safest for the environment, as there is no mining of ore mass. "Our ore horizons are limited by thick aquitards composed of clay and gypsum. This is an insurmountable barrier for technological solutions – there are no spills, and the entire technological process takes place underground at a great depth," he explains.
On the surface, we only see pipes and wires. "Uranium does not come into contact with the environment. Moreover, it is in a dissolved state – it cannot be lost. Therefore, the entire process is strictly controlled. This is a cutting-edge uranium extraction technology. CAP was at the forefront of developing this method. Kazatomprom's developments are the best in the world, which is why we still hold the leading position, primarily ensured by our cost-effectiveness and production safety," concludes the head of the extraction department at SP Inkai.
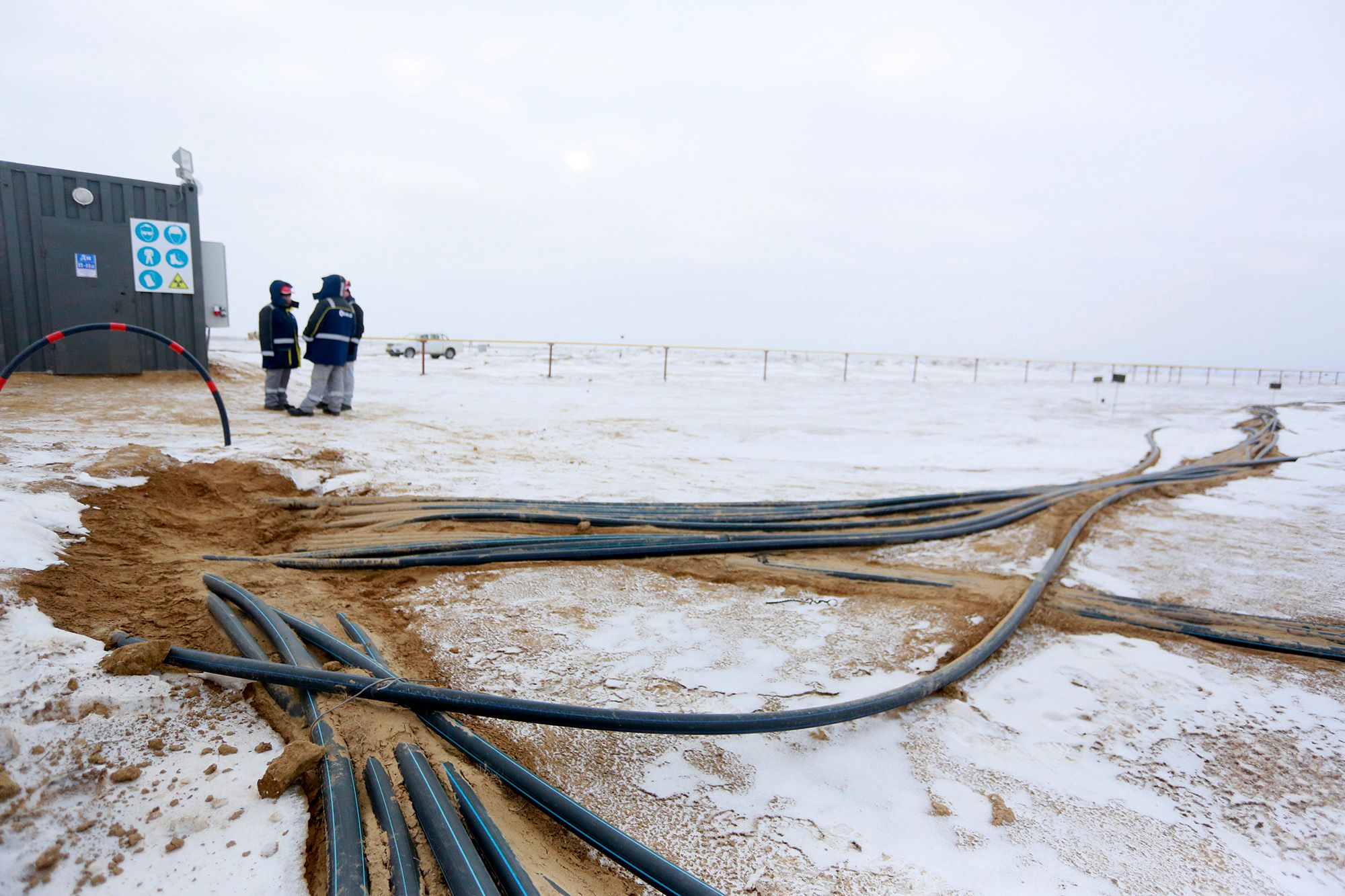
At the geotechnological polygon (GTP), which stretches over 25 km in length and 12 km in width, 105 people are employed. "They service the GTP equipment, monitor the operation of geotechnological wells, responsible units, and ensure safe production activities. There are no moving mechanisms here; all automation is focused on controlling the technological process," summarizes the speaker.
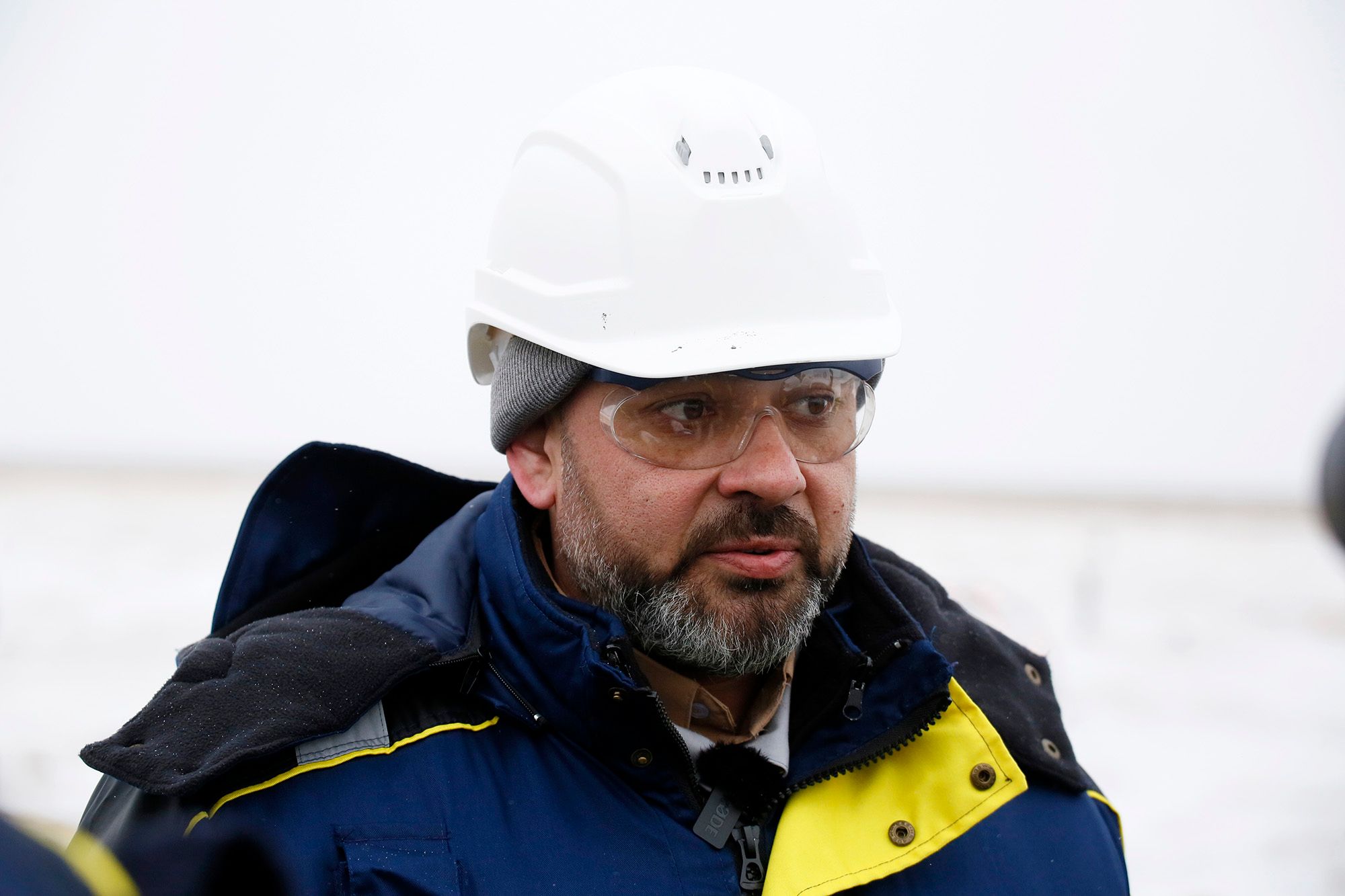
Stepan Tretyakov, head of the extraction department at SP Inkai
"The daily volume of productive solution extraction is about 90,000 cubic meters, from which we extract approximately 8.5-10 tons of uranium. The Inkai deposit has 140-150 thousand tons of uranium ready for development, which is covered by the contract of SP Inkai. The remaining reserves are projected until 2056. This is the largest deposit in Kazakhstan in terms of explored reserves," reports Stepan Tretyakov. In addition to the Turkestan region, uranium is also extracted in the Akmolinsk and Kyzylorda regions, he adds.
Next Stage: Processing
Journalists also visited the productive solution processing workshop (CPS) at the Satellite-2 site and learned what happens to the productive solution containing uranium after it is brought from the geotechnological polygon (GTP). Before visiting the CPS, we underwent an introductory briefing and donned personal protective equipment: suit, helmet, goggles, boots, and gloves.
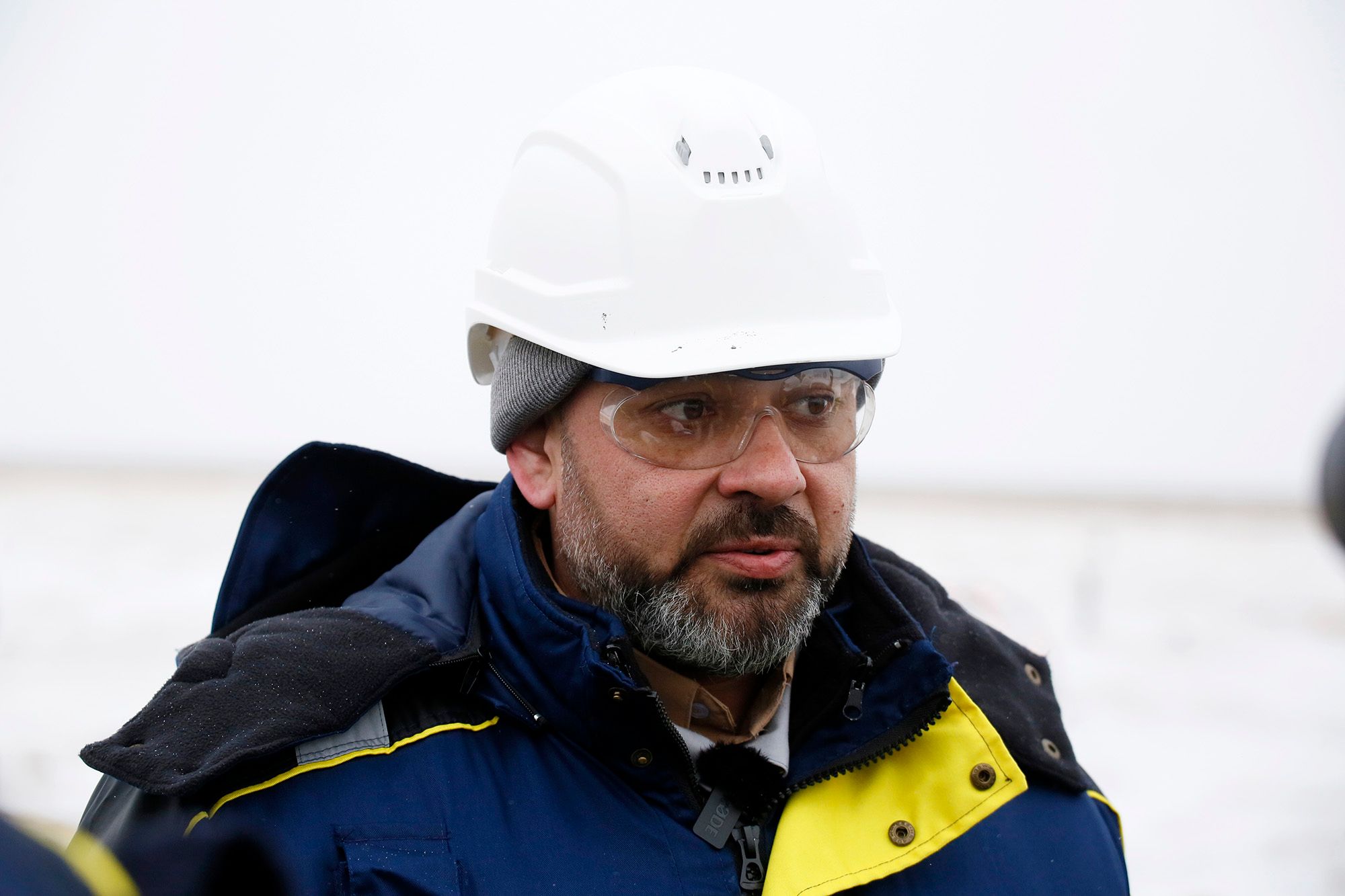
The head of the processing department at SP Inkai, Aibek Aydymbekov, provided more details about the technological process: "The Satellite-2 site processes up to 1,000 tons of uranium per year. Here, ion-exchange resin seemingly absorbs uranium. Then, we remove and concentrate what has been absorbed. After that, the concentrated solutions are sent to the main processing plant (MPP). There, precipitation, filtration, and drying processes occur. After drying, the final product – uranium peroxide (which contains 70-72% uranium) – is packaged, loaded into regular steel barrels, and sent to the consumer."
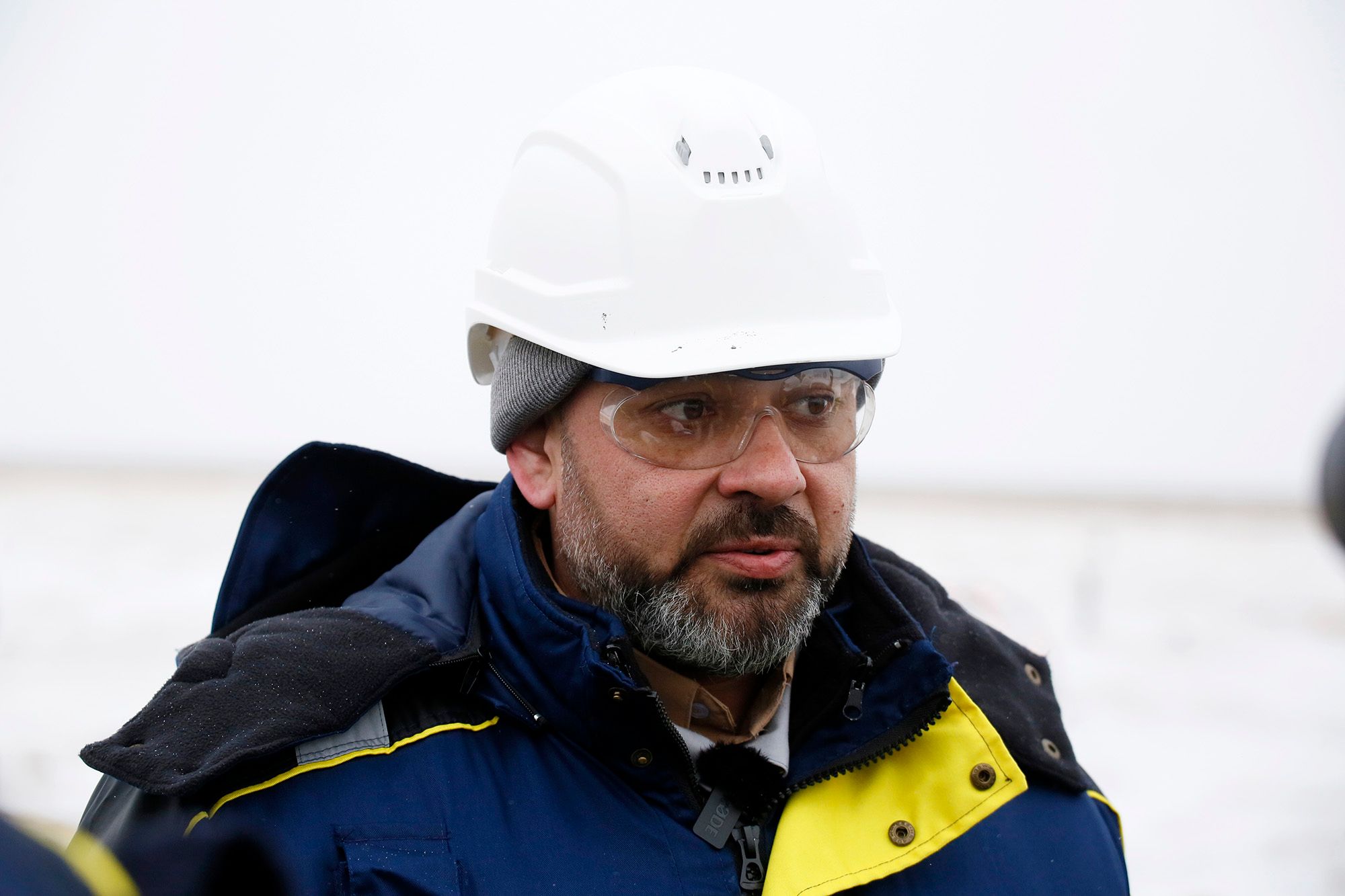
Ion-exchange resin
Thus, a semi-finished product – commercial desorbate – is produced at the Satellite-2 site. "This is a liquid with a uranium content of about 90 grams per liter, a 10% solution, which then undergoes further stages," explains Aibek Aydymbekov. Annually, SP Inkai processes 30-35 million cubic meters of productive solution, he adds.
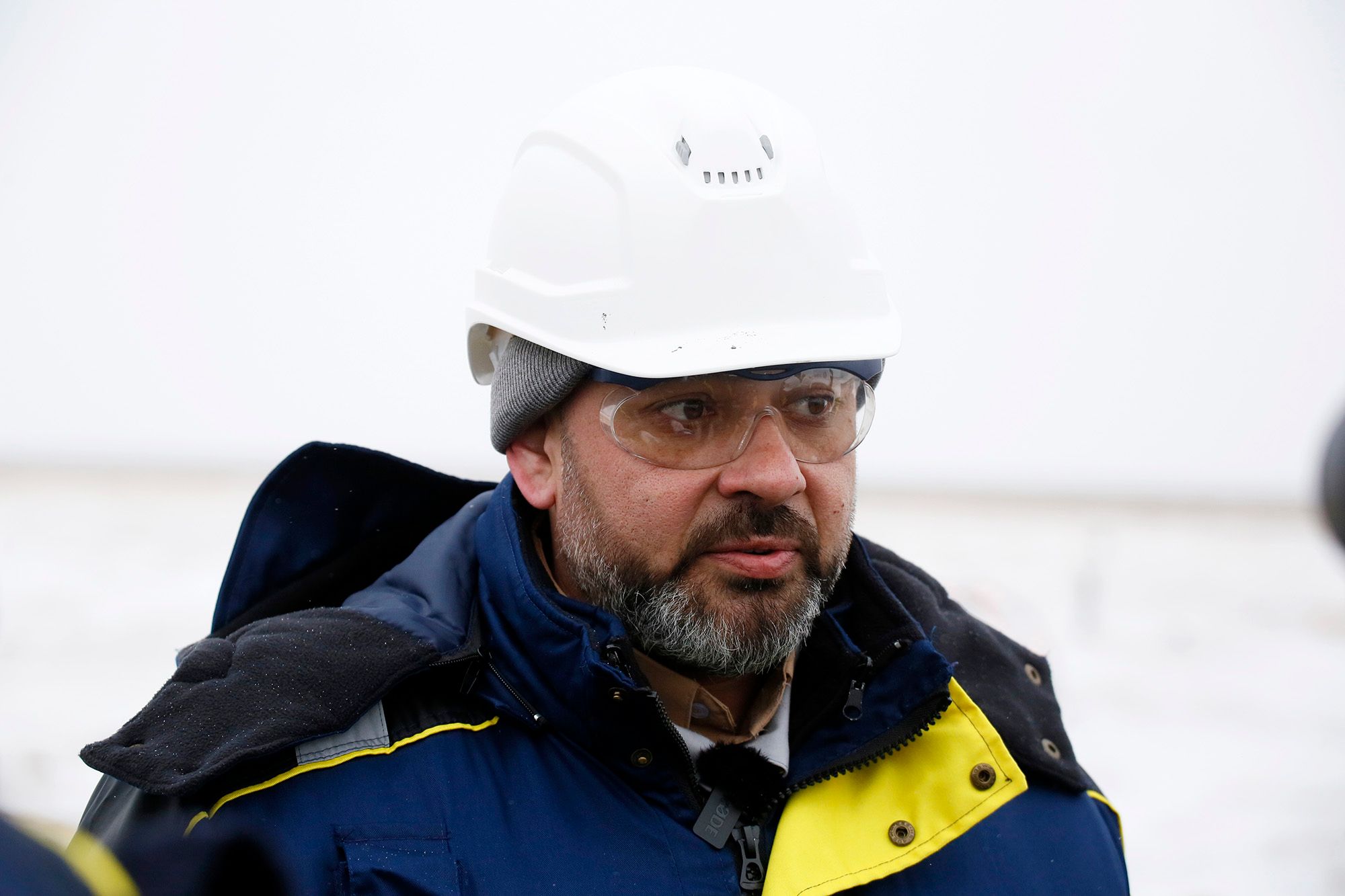
Aibek Aydymbekov, head of the processing department at SP Inkai
According to the speaker, the total number of employees at SP Inkai during this production stage (from the processing of productive solution to the release of the final product – Ed.) is 116 people.
"There are four main reagents used at all stages, from uranium extraction to the release of the final product. These are sulfuric acid (92.5%), ammonium nitrate (78.8%), hydrogen peroxide (60%), and anhydrous ammonia (99.9%)," notes the head of the processing department at SP Inkai.
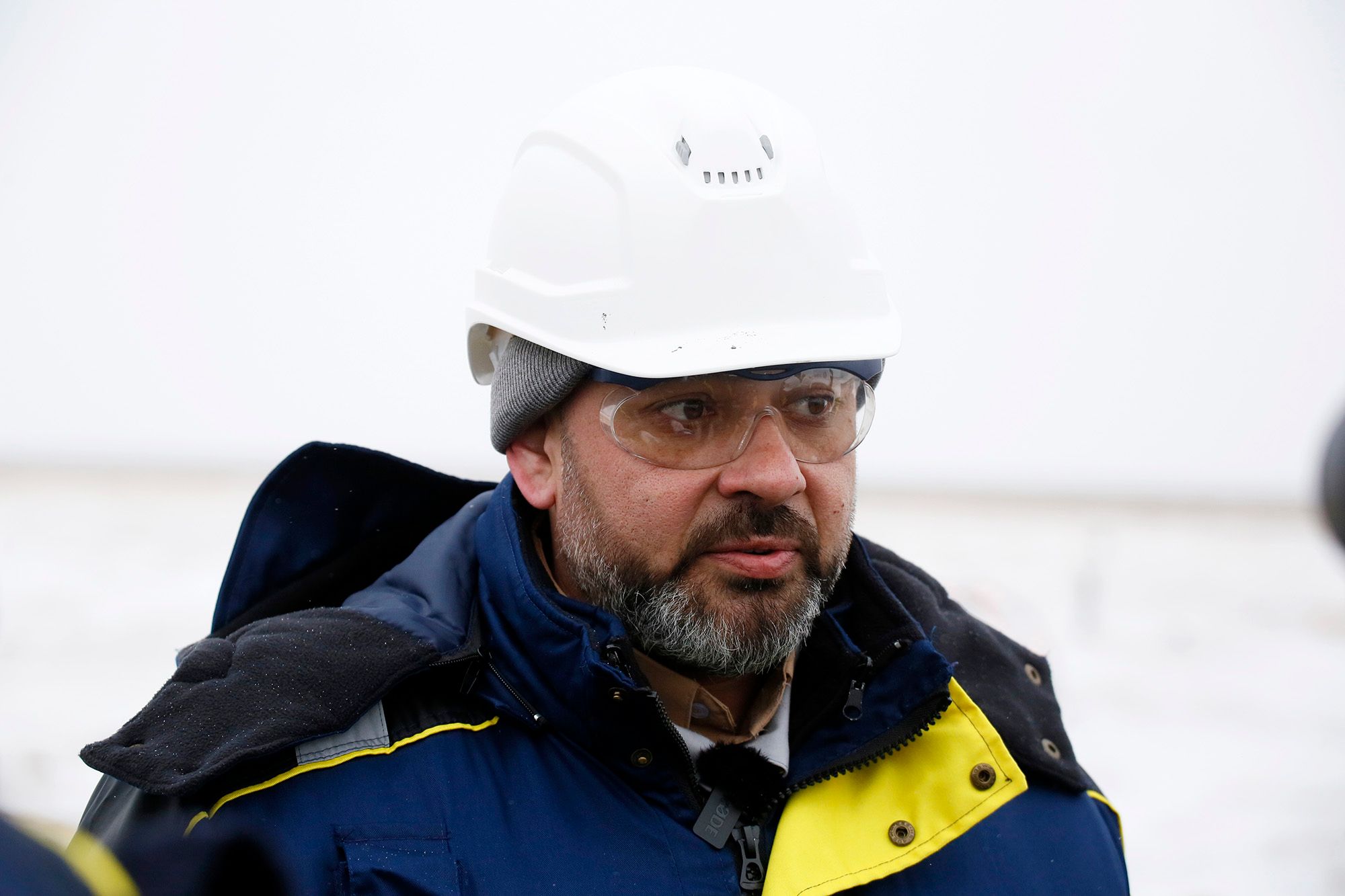
"In our company, the productive solution processing workshop (CPS) processes the productive solution that comes to us from the geotechnological polygon – it undergoes technological processes of sorption and desorption. And uranium in the form of commercial desorbate is sent for processing to the main processing plant. As you can see, we have automated all the main technological processes, which are controlled from the dispatch point," says Almas Abdiyanov, head of the process optimization department at CPS.
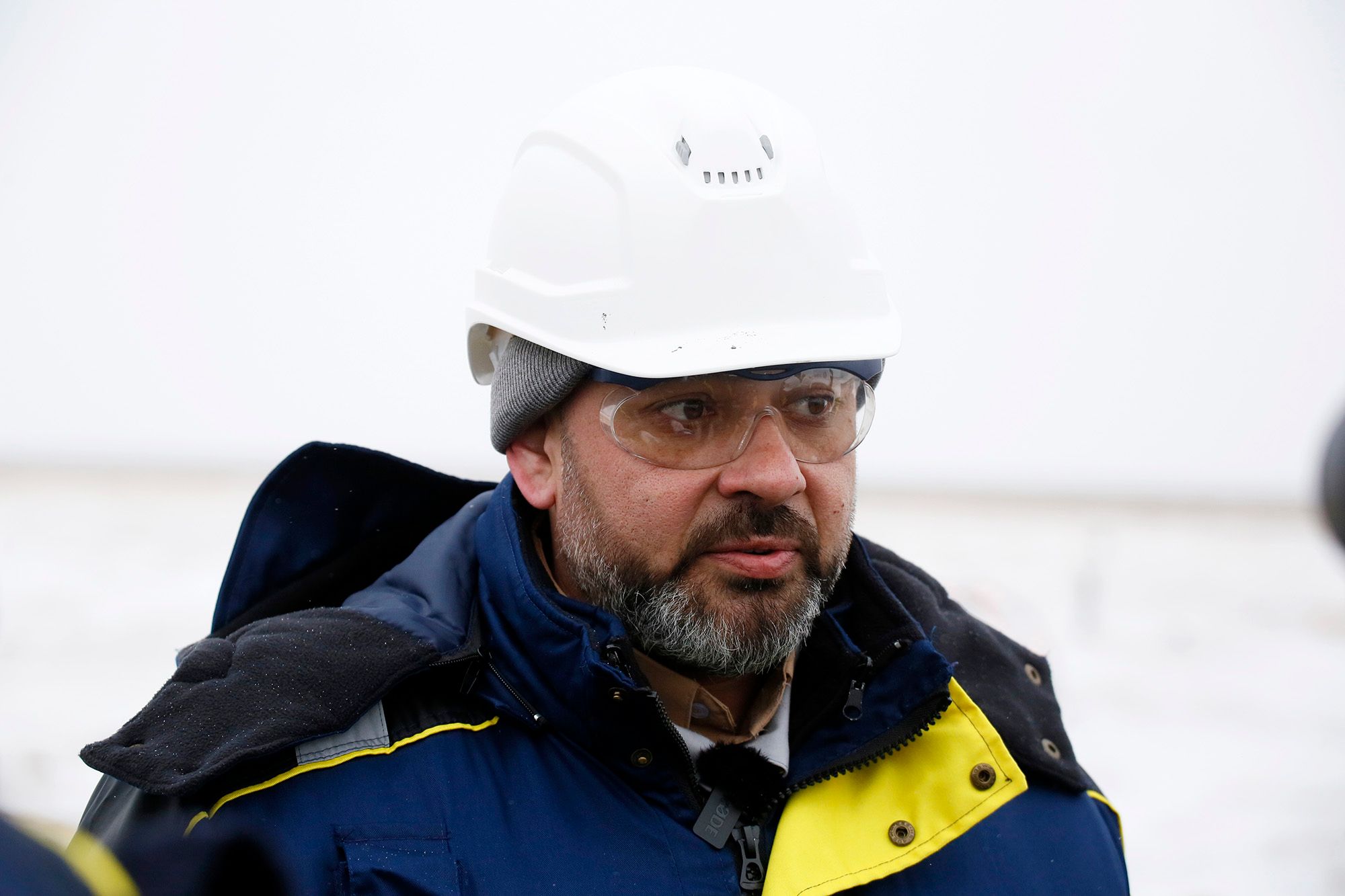
Beksultan Ilyas, operator of the productive solution processing workshop
Pre-Uranium Extraction Stage
Upon arrival at Satellite-2, journalists were also shown a mobile logging station (MLS) with hydraulic drive. It is designed for conducting geophysical surveys in wells. The logging station allows for obtaining information about the geological structure, the location of uranium ore, and the overall condition of the well. The company reports that there are a total of five such stations at SP Inkai.
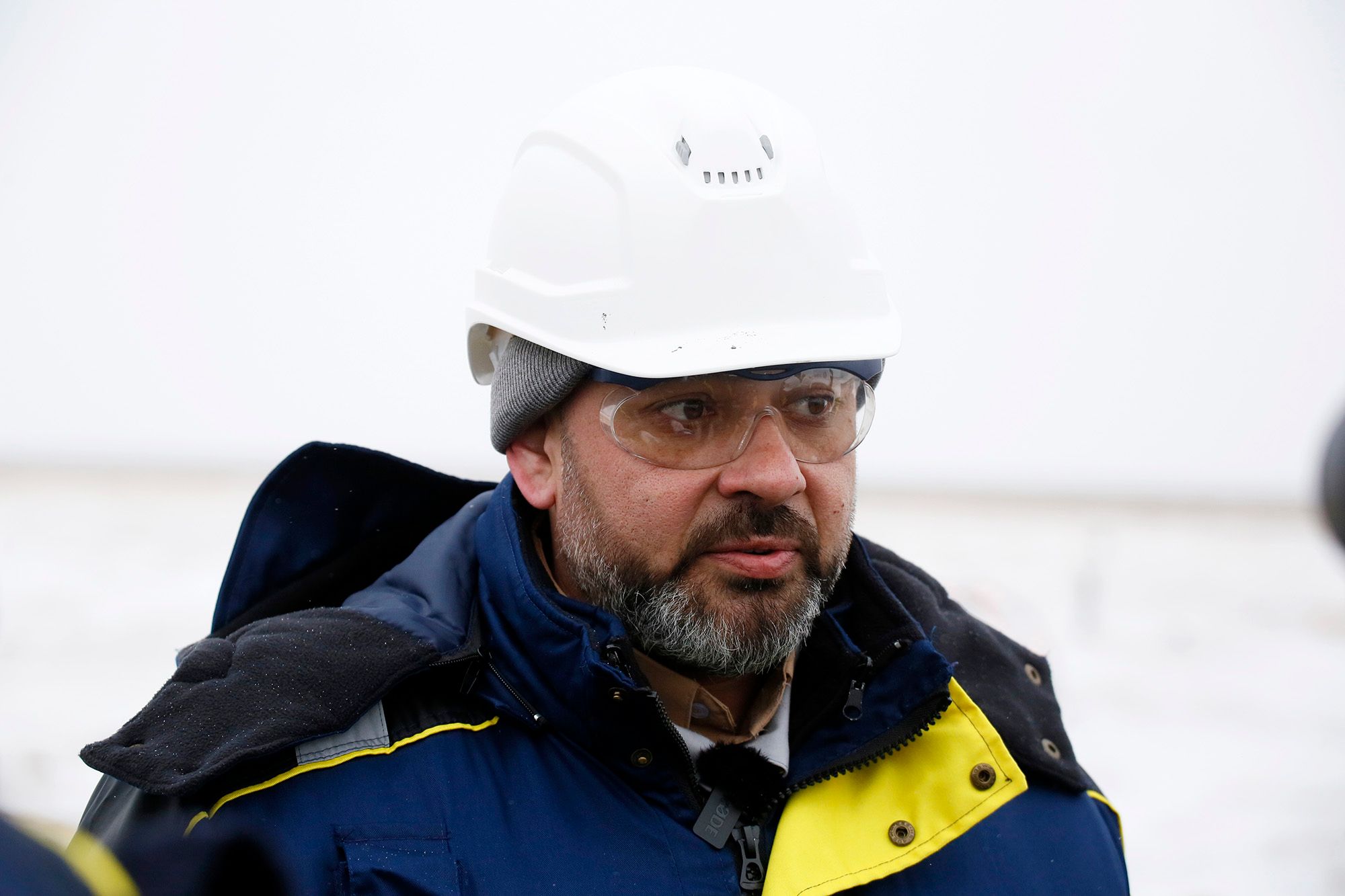
In 2022, SP Inkai specialists implemented a digital comprehensive well device to reduce the time for conducting geophysical surveys. The company reports that this allowed for performing primary logging in one descent-ascent, rather than in two or three, as is the case in most instances.
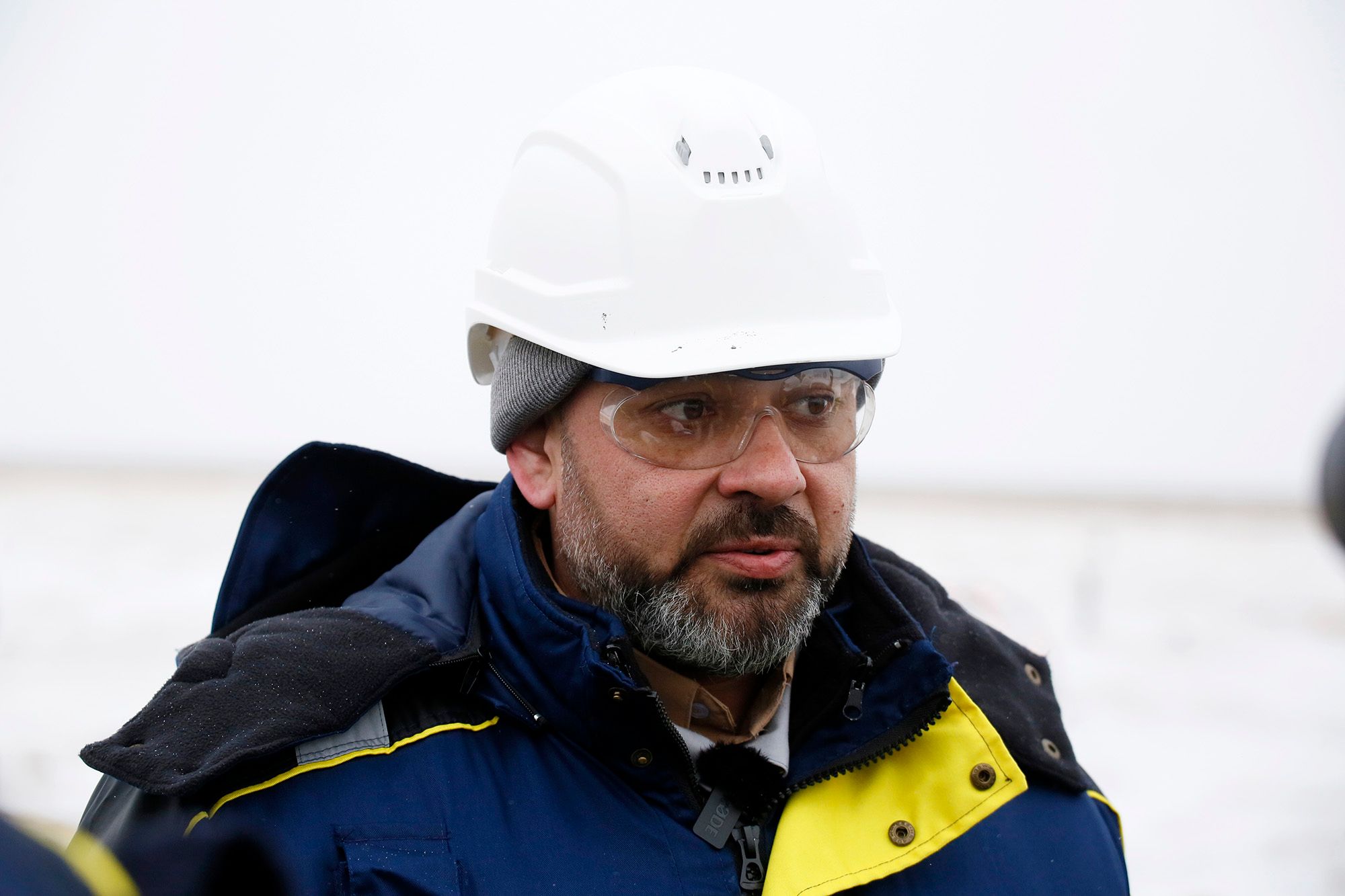
"In Kazakhstan, only we have such a device. The digital comprehensive well device simultaneously measures four parameters: radiation – determined by gamma logging